Case Study: Extending Tool Life with Böhler K390 Microclean
Client
Major Automotive Pressings Manufacturer
Objective
Increase punch tool life, reduce cost-per-part, and minimise tool changeovers in high-volume AHSS stamping.
Background
- Tool Application: Punching AHSS for automotive structural components
- Original Tool Material: M2 High Speed Steel (HSS) with CrN coating
- Tool Hardness: 61–63 HRC
- Baseline Tool Life: 120,000 parts
- Failure Mode: Wear and edge chipping
- Tool Cost: £160 per punch
- Regrinds Possible: None
Project Goal
Achieve over 1 million parts per punch through advanced tool material selection and optimised maintenance (regrinding).
Material Recommendation
Recommended Material: Böhler K390 Microclean
- High-performance powder metallurgy (PM) tool steel
- Excellent wear resistance and toughness
- Compatible with existing CrN coating
- Allows up to 3 regrinds while maintaining integrity
Trial Results
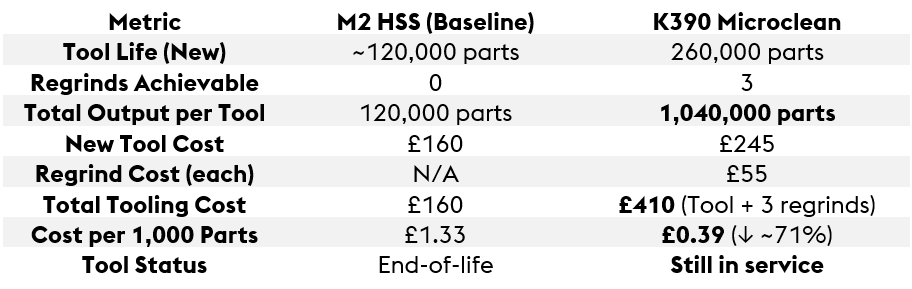
Key Observations
- Tool life extended by 8.6×
- Chipping managed effectively through planned regrinds
- Consistent part quality throughout life cycle
- Tool changeovers reduced by 75%, boosting uptime
- Significant cost savings: ~71% reduction in cost per part
Conclusion
Increase punch tool life, reduce cost-per-part, and minimise tool changeovers in high-volume AHSS stamping.
Ready to #ChallengeUs?
Contact us for further information
Fields marked with * are mandatory.